Professional Tips for Choosing the Right Metal Stamping Providers for Your Requirements
Professional Tips for Choosing the Right Metal Stamping Providers for Your Requirements
Blog Article
Advanced Techniques in Metal Stamping for Accuracy Production
In the world of precision production, the development of metal marking methods has been a crucial pressure in achieving unparalleled degrees of accuracy and performance. As sectors continually require better resistances and intricate designs in their steel parts, the quest for innovative techniques in steel stamping has intensified. From the use of innovative multi-stage marking procedures to the combination of advanced automation innovations, the landscape of steel marking is undertaking an extensive makeover. In this dynamic arena, the merging of technology and precision is reshaping the possibilities of what can be achieved in steel fabrication.
Advanced Multi-Stage Stamping Procedures
Reviewing the intricacies of advanced multi-stage stamping processes exposes the innovative strategies used in modern manufacturing practices. Metal Stamping. Multi-stage stamping is a complex process that involves several steps to change a level sheet of steel right into a last stamped product. Using progressive dies, where different operations are done at each phase of the marking process, enables high precision and effectiveness in the production of intricate metal parts
During the first stages of multi-stage marking, the flat metal sheet is fed right into the marking press, where a series of dies are utilized to reduce and form the material. Subsequent stages include additional forming, flexing, and punching operations to additional improve the part. Each phase is thoroughly created to build on the previous one, bring about the development of complicated geometries with limited resistances.
Advanced multi-stage stamping procedures need a high degree of competence and accuracy to make sure the top quality and consistency of the stamped components. By using innovative equipment and tooling, makers can create a wide variety of steel elements with efficiency and precision.
Precision Tooling Innovations
Precision tooling innovations have actually reinvented the metal marking industry, improving performance and quality in producing procedures. CNC systems allow for complex layouts to be translated straight right into tooling, guaranteeing precision and repeatability in the marking procedure.
Furthermore, the integration of sensors and real-time tracking abilities in precision tooling has allowed makers to identify and address issues promptly, minimizing downtime and decreasing scrap rates. By incorporating smart technology into tooling, drivers can maximize criteria such as stress, rate, and positioning during the stamping operation, resulting in boosted item high quality and boosted efficiency.
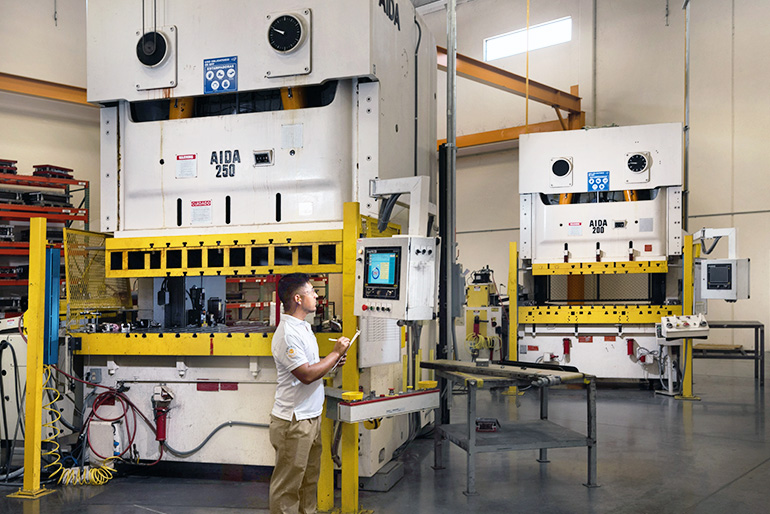
Automation in Metal Stamping
The evolution of precision tooling innovations in the steel marking market has led the way for substantial improvements in automation, transforming the manufacturing landscape towards raised effectiveness and efficiency. Metal Stamping. Automation in metal marking includes making use of sophisticated equipment and robotics to do different tasks commonly executed by human operators. This change in the direction of automation provides various advantages, consisting of boosted precision, faster manufacturing visit this site cycles, and minimized labor costs
One trick element of automation in steel marking is the implementation of computer system mathematical control (CNC) systems, which enable accurate control over the stamping procedure. CNC innovation permits the development of complex and detailed metal get rid of regular quality. Furthermore, automated systems can be set to run continually, causing greater outcome prices and shorter preparations.
Additionally, automation improves work environment safety by minimizing hands-on handling of heavy materials and minimizing the danger of crashes (Metal Stamping). As making sectors remain to embrace automation, the future of steel marking holds excellent look these up promise for even higher efficiency and development
High-Speed Stamping Techniques

Among the key benefits of high-speed marking strategies is the capacity to create a large volume of parts in a shorter amount of time compared to traditional stamping approaches. This raised productivity not only allows manufacturers to fulfill tight manufacturing deadlines yet also enables expense financial savings with economic climates of scale. In addition, high-speed marking can help in reducing product waste by enhancing the material usage throughout the marking process.
Moreover, high-speed stamping techniques frequently incorporate innovative attributes such as fast die modification systems and real-time monitoring capabilities, better boosting the general efficiency and flexibility of the steel stamping process. As modern technology proceeds to advancement, high-speed stamping is anticipated to play a vital function in driving the future of precision production.
High Quality Control in Stamping Operations
Reliable quality assurance measures are crucial for making certain the dependability and consistency of steel stamping procedures. Quality control in marking operations entails a series of organized procedures targeted at identifying and stopping defects in the made components. One critical aspect of top quality control in metal marking is making use of innovative evaluation strategies such as optical evaluation systems and coordinate determining makers (CMMs) to validate the measurements and resistances of stamped parts.
In addition, quality assurance actions in marking operations frequently consist of the implementation of analytical process control (copyright) methods to check the production procedure in real-time and ensure that it stays within appropriate limitations. By examining information and determining trends, producers can proactively address any deviations from the wanted quality criteria.
Furthermore, quality control in metal stamping operations additionally entails complete product testing to make certain that the raw products utilized satisfy the called for requirements for the stamping procedure. This may consist of carrying out material hardness examinations, tensile stamina tests, and dimensional inspections to guarantee the quality and honesty of the stamped components. Overall, applying robust quality assurance measures is crucial for accomplishing high-quality stamped parts regularly.
Conclusion
To conclude, advanced additional reading methods in steel stamping play an important function in accuracy production procedures. With multi-stage marking procedures, cutting-edge tooling options, automation, high-speed strategies, and rigorous quality control steps, makers can attain greater levels of accuracy and effectiveness in their procedures. These advancements in metal marking modern technology have actually made it possible for companies to produce complex get rid of limited tolerances, eventually causing boosted item top quality and client satisfaction in the manufacturing market.
Report this page